炭素繊維強化プラスチック(CFRP・CFRTP)の成型法って何?
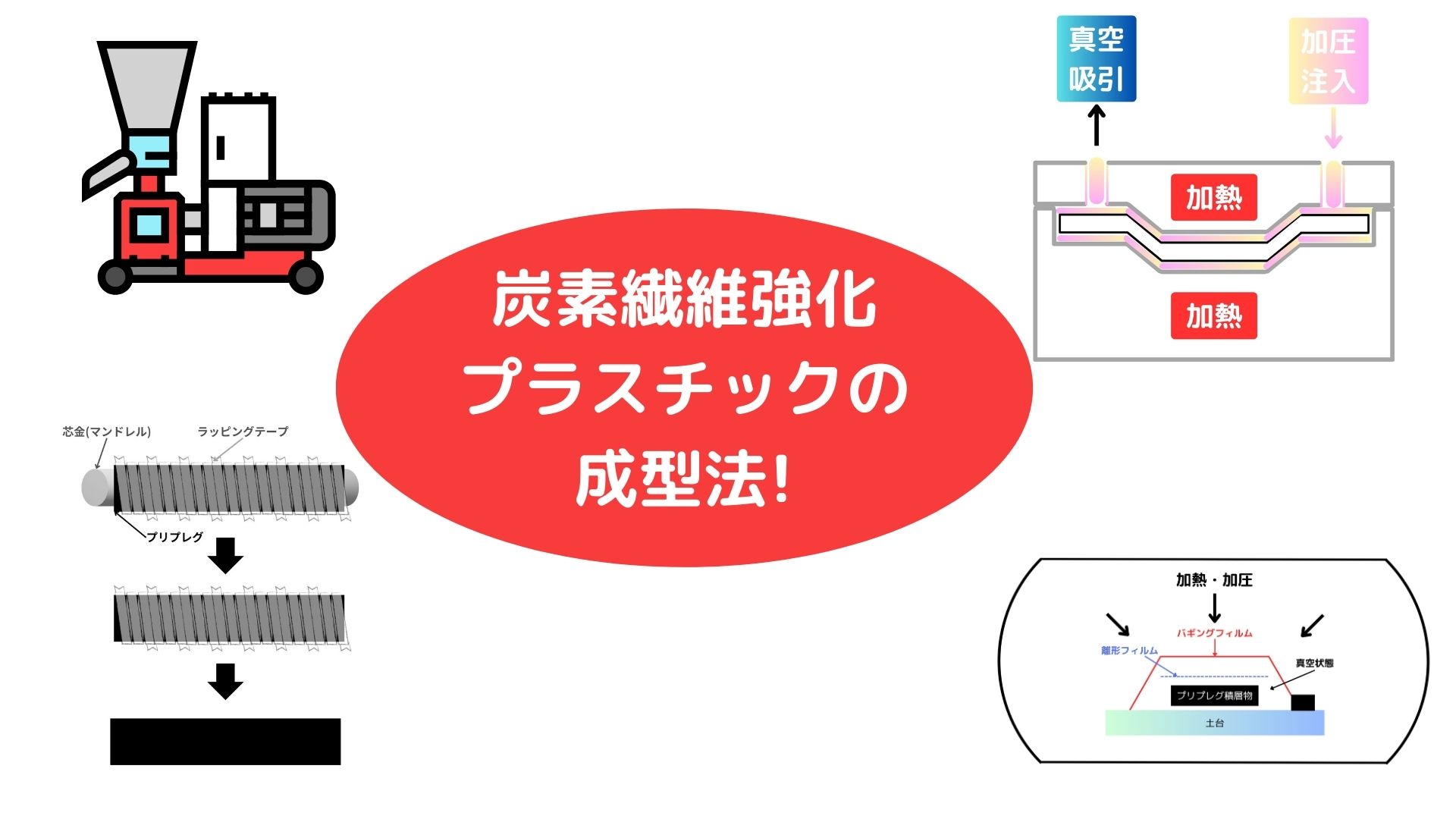
技術ブロガーのスーです
本記事では、炭素繊維強化プラスチックの成型法について紹介します
炭素繊維強化プラスチックには様々な成型法があり、作るものの大きさや必要な強度によって適切な成型法が変わります
加えて、量産性が良い成型法もあればほとんど手作業で行われるような成型法もあり、作るものに対して適切な成型法を選択することが重要となります
本記事では
「部品の軽量化のために炭素繊維強化プラスチックを使用したいけどどの成型法が良いの?」
「高い力学的特性が得られる成型法が知りたい!」
「最新の成形法ってあるの?」
「量産性が良い成型法が知りたい!」
などの疑問にお答えします
- 炭素繊維強化プラスチックの成型法の種類
- 各成型法の特徴と生産可能な形状
- 各成型法の量産性
- 各成型法で製造されている具体例
オートクレーブ法って何?
オートクレーブ法はCFRPの製法としては広く知られており、多種多様な部品の製造に使用される方法です
オートクレーブ法で用いられる中間基材は、プリプレグです
下記の公式JAXAチャンネルで紹介されているオートクレーブ法の動画を見てみて下さい
オートクレーブ法
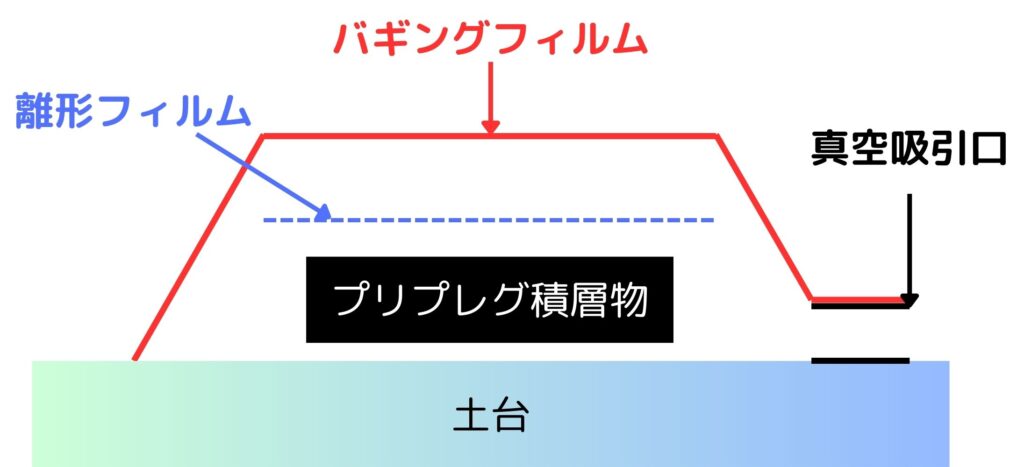
↓

①裁断したプリプレグを賦形(積層)する
②土台の上に積層部を載せ、上から離形フィルム・バギングフィルムを被せる
③真空吸引口から吸引し、真空状態にする
④③をオートクレーブ(圧力釜)の中に入れセットする
⑤加熱・加圧して、樹脂を硬化させる
メリット・デメリット
オートクレーブ法のメリット
- 真空状態で焼成するため、ボイドが形成されにくく高品質な成型物が得られる
- オートクレーブ内で全体(360°)から加圧されるため、高品質な成型物が得られる
- 複雑な形状を成型できる(板状・円筒形状共に)
- オートクレーブに入るサイズであれば、大きなサイズでも成型可能
オートクレーブ法のデメリット
- 多額の設備投資が必要
- 成型に手間がかかるので、成形コストが高い
- 手作業が多く、大量生産には向かない
総合評価
品質:
力学的特性:
成型コスト:
量産性:
成型サイズ:
成型可能な形状の自由度:
寸法精度:
オートクレーブ法で製造されている具体例
航空機用部材
解説
オートクレーブ法はメリット・デメリットがハッキリしていて、コストや量産性は乏しくてもよいけど高品質なものや大きな部品が欲しい!という場合に適しています
代表例は航空機用部材であり、人命が関わるため安定した高品質や大サイズの成型物が求められます
シートワインディング法って何?
シートワインディング法に使用される中間基材はプリプレグです
”シート”はプリプレグのことを指します
シートワインディング法で成型される代表例の釣竿の成型動画を見てみて下さい
シートワインディング法
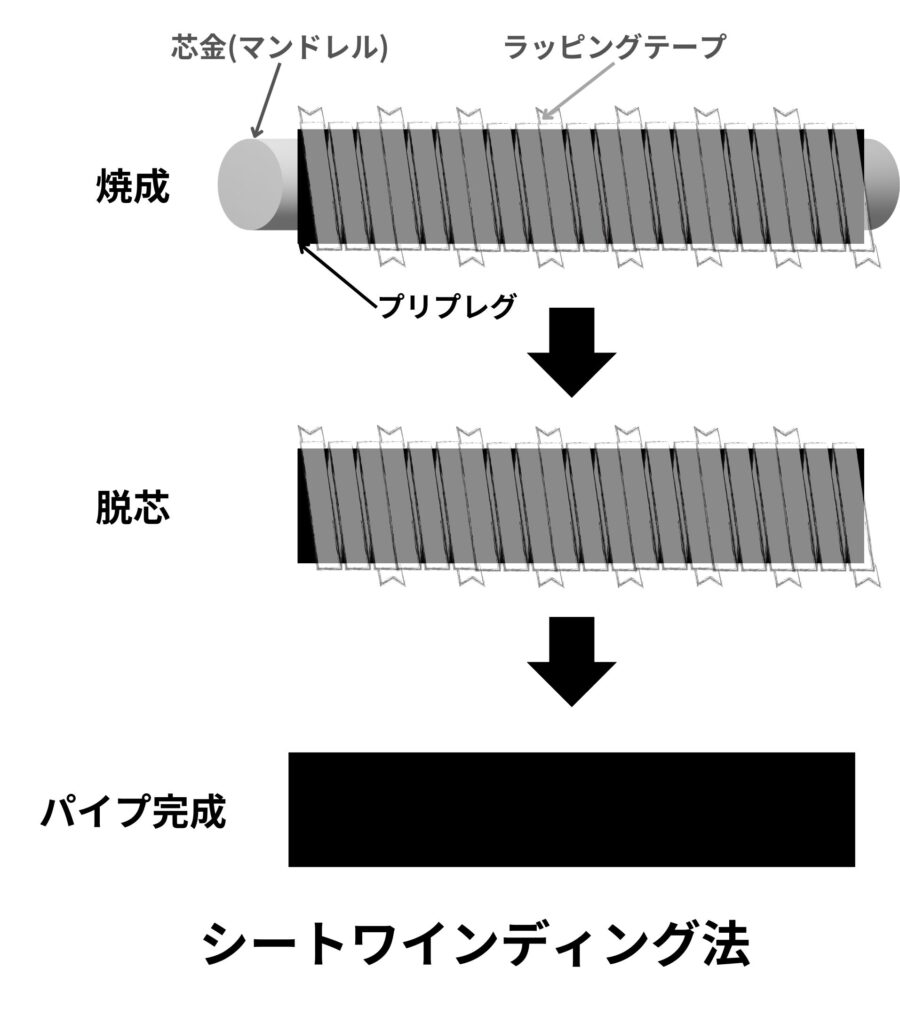
①芯金と呼ばれる、金属製の棒にプリプレグを賦形(ふけい: プリプレグを型に沿わせること)
②ラッピング
③焼成し、エポキシ樹脂を硬化
④ラッピングテープを外す
⑤芯金を取り外す(脱芯)
メリット・デメリット
シートワインディング法のメリット
- 工程が比較的に簡単なので、量産性が良い
- 芯金を利用するため、内径の寸法精度が良い
- 円筒形状が作成可能
- 様々な繊維方向を組み合わせることが可能
シートワインディング法のデメリット
- 芯金の抜きテーパが必要なので異形状の作成が不可
- 後加工なしだと外径が安定しない
- 円筒形状しか作成できない
総合評価
品質:
力学的特性:
成型コスト:
量産性:
成型サイズ:
成型可能な形状の自由度:
寸法精度:
シートワインディング法で製造されている具体例
釣竿・ゴルフシャフト
解説
シートワインディング法を成型方法として採用するかどうかの判断基準として最も簡単な事は、作りたいものが円筒パイプであるかどうかです
成形ノウハウが蓄積されている成型方法なので、必要な性能に合わせて繊維配向を配置することも可能ですし、量産性も高い成型方法です
サイズも2mくらいまでなら問題なく成型できます
円筒パイプを作りたいなら、シートワインディング法を選ぶべきでしょう
プレス成型って何?
プレス成型に用いられる成型法は、プリプレグとSMC(シートモールディングコンパウンド)です
プレス成型

①裁断したプリプレグを積層する
②下型に沿うようにプリプレグを賦形する
③金型を閉じ、加圧・加熱
④脱型
メリット・デメリット
プレス成型のメリット
- 金型を温めたまま生産できるため、高サイクルタイム
- 全ての面が金型で成型されるため、寸法精度が良い
- 板形状が作りやすい
プレス成型のデメリット
- プレス機が必要
- 金型の抜きテーパを考慮する必要がある
- 真空状態での成型ではないので層間や表面にボイドが形成される可能性がある
総合評価
品質:
力学的特性:
成型コスト:
量産性:
成型サイズ:
成型可能な形状の自由度:
寸法精度:
プレス成型法で製造されている具体例
CT天板
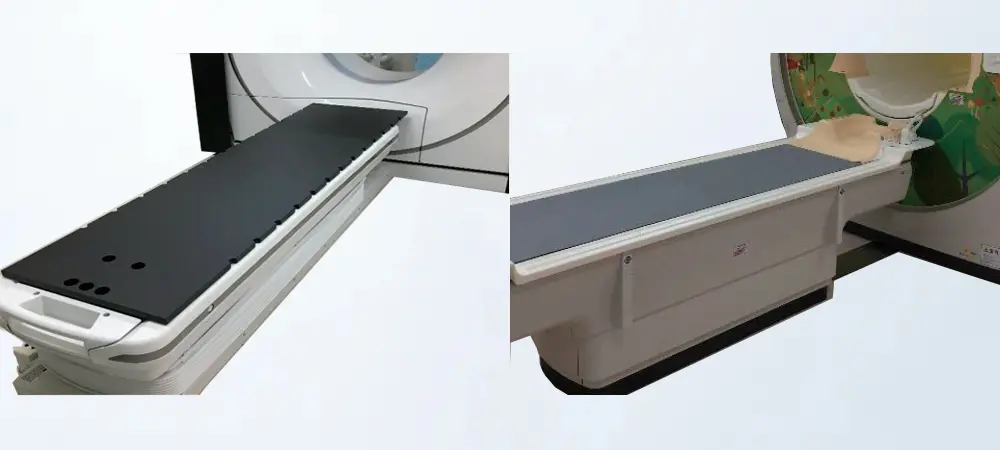
引用: 治療計画用CTカーボン天板・MRI用フラットマット | フジデノロ株式会社 (fujidenolo.co.jp)
解説
プレス成型の最大のメリットは、量産性です
成型サイズは、大サイズの金型をプレス可能な設備があればかなり大きなサイズまで成型可能です
全面金型での成型となるため寸法精度は良いですが、一方で抜きテーパを考慮すると成型可能な形状に制限があります
内圧成型って何?
内圧成型で使用される中間基材はプリプレグです
内圧成型で作られる代表例である自転車のカーボンホイールの成型動画です
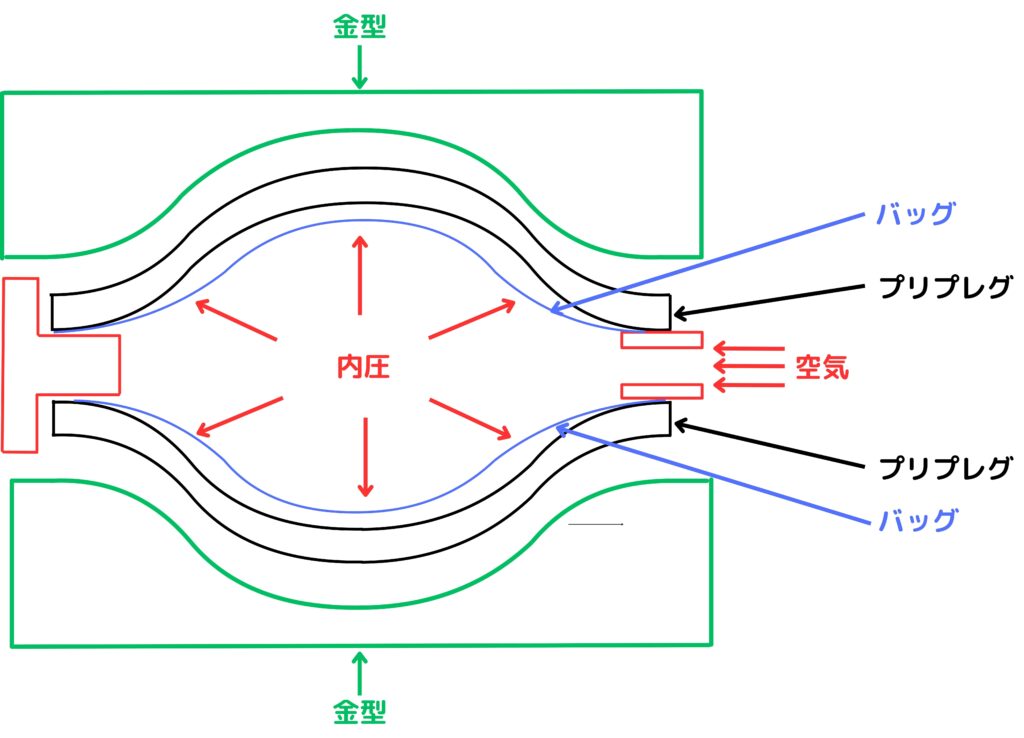
①裁断したプリプレグを積層する
②ある程度金型形状に沿うように賦形する
③バッグ(ナイロンビニールやシリコン製)をプリプレグの内側に通す
④バッグの片側をシールし、注入孔から空気を入れる
⑤バッグが膨らむことによって内側から加圧する
⑥焼成後、脱型
メリット・デメリット
内圧成型のメリット
- 複雑形状の作成が可能
- 円筒形状の作成が可能
内圧成型のデメリット
- 内径側には金型がないので、内径側の寸法精度が低い
- 複雑な形状になると、賦形に時間がかかる
総合評価
品質:
力学的特性:
成型コスト:
量産性:
成型サイズ:
成型可能な形状の自由度:
寸法精度:
内圧成型法で製造されている具体例
カーボンホイール・テニスラケット
解説
内圧成型は内側からの空気圧で成型する方法であるため、他の成型法ではアンダー形状となるような形状でも作成可能です
必然的に作成するものの形状が複雑になることが多く、賦形(レイアップ)に時間を要することなどから成形コストは高くなります
また、内圧を受ける面には金型がないため、寸法精度が悪くなることも弱点です
フィラメントワインディング法って何?
フィラメントワインディング法は中間基材を用いず、炭素繊維そのものを使用する成型法です
フィラメントワインディング法で圧力容器を成型する動画を紹介します
フィラメントワインディング法
※絵が難しいので東レカーボンマジック株式会社の図を引用させていただきました
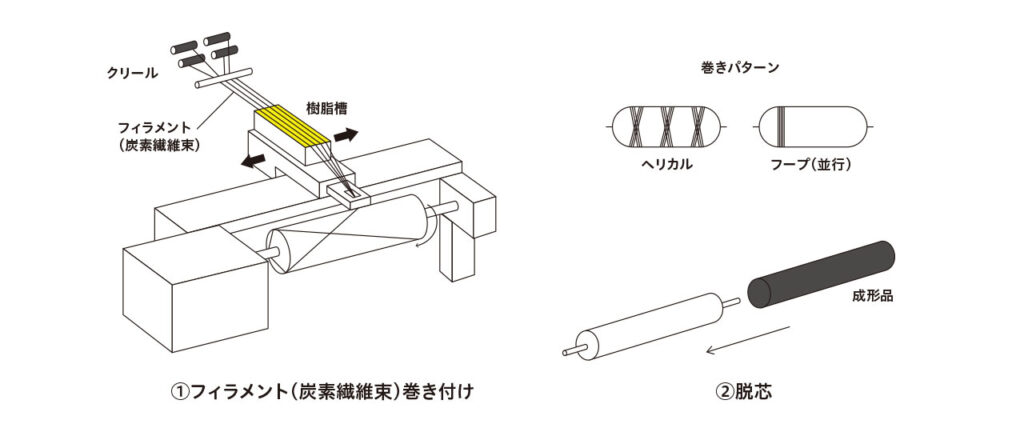
引用: CFRPの成形方法について概要や工程を詳しく解説 (carbonmagic.com)
①炭素繊維束を引き揃える
②炭素繊維束を樹脂槽に通過させる
③炭素繊維束をテンションをかけながら、芯金(マンドレル)に巻きつける
④焼成炉に入れて樹脂を硬化させる
⑤焼成後、脱芯
メリット・デメリット
フィラメントワインディング法のメリット
- 自動化された成型方法のため、量産性が良い
- 品質が安定する
- 高い力学的特性
フィラメントワインディング法のデメリット
- 多額の設備投資が必要
- 形状の自由度が低い
総合評価
品質:
力学的特性:
成型コスト:
量産性:
成型サイズ:
成型可能な形状の自由度:
寸法精度:
フィラメントワインディング法で製造されている具体例
圧力容器
解説
成形の方法としては芯金(マンドレル)を使用することなど、シートワインディング法と似ている部分があります
この成型法の欠点は、シートワインディング法と同じく円筒形状しか成型できない事です
一方で、長所は賦形の工程が自動化されていることであり、量産性が良いことや品質が安定することです
炭素繊維強化プラスチックの成型法の中では自動化されていることは珍しいため、大きな長所と言えます!
レジントランスファーモールディング(RTM)法って何?
レジントランスファーモールディング(RTM)法は、織物(クロス)などのドライ中間基材を用いる成型法です
日産のRTM法を用いた自動車部品の成型の様子がYoutubeにあったので紹介しておきます
レジントランスファーモールディング(RTM)法
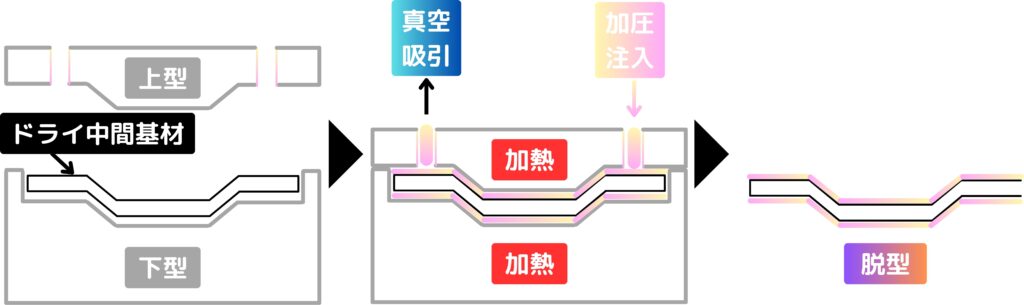
①ドライ中間基材を金型に賦形(プリフォーム)する
②金型を閉じる
③樹脂と硬化剤を混ぜる
④樹脂を高圧で注入し、金型を加熱
⑤焼成後、脱型
メリット・デメリット
レジントランスファーモールディング(RTM)法のメリット
- 高サイクルタイムによって、量産性がよい
- 品質が高品質で安定する
- 複雑形状の成型が可能
レジントランスファーモールディング(RTM)法のデメリット
- 多額の設備投資が必要
- 金型の抜きテーパを考慮する必要がある
- 樹脂の流動性が悪いとボイドが発生する
- 高圧で樹脂を注入する際に、炭素繊維が蛇行する
総合評価
品質:
力学的特性:
成型コスト:
量産性:
成型サイズ:
成型可能な形状の自由度:
寸法精度:
レジントランスファーモールディング(RTM)法で製造されている具体例
自動車部品
解説
先に紹介したプレス成型法と似ていますが、プレス成型法では樹脂含侵中間基材を使用するのに対して、RTM法ではドライ中間基材を使用する点が大きく違います
この違いによって大きく変わる点は、成形可能な形状の自由度です
プレス成型は金型の圧力のみで、樹脂含侵中間基材(プリプレグやSMC)に含まれる樹脂を流動させるため、板形状の成形がメインとなります
一方で、RTM法では高圧で樹脂を注入し樹脂流動させるため、3次元的な形状も成型可能です
プルトージョン(引き抜き)法って何?
プルトージョン(引き抜き)法は中間基材を用いず、炭素繊維そのものを使用する成型法です
※絵が難しいので東レカーボンマジック株式会社の図を引用させていただきました
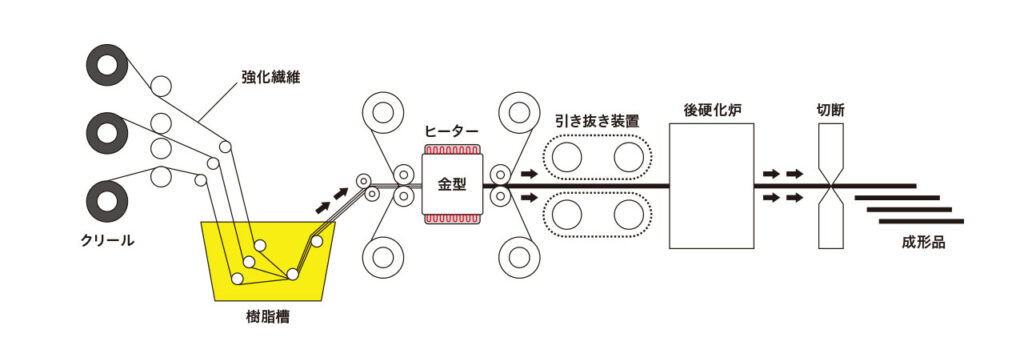
引用: CFRPの成形方法について概要や工程を詳しく解説 (carbonmagic.com)
①炭素繊維束をボビンから引き出す
②炭素繊維を樹脂槽に通して樹脂を含浸させる
③樹脂を含浸させた炭素繊維を金型に引き込む
④金型内で加熱し、樹脂を硬化させる
⑤硬化した成形品を連続的に引き抜く
⑥所定のサイズで切断
メリット・デメリット
プルトージョン(引き抜き)法のメリット
- 連続的な成型が可能なため、量産性が良い
- 成型時の無駄な材料が少ない
- 品質が安定している
プルトージョン(引き抜き)法のデメリット
- 成形可能な形状に制限がある(断面形状が一定でなければならない)
- 多額の設備投資が必要
- 一方向にしか繊維を配置させることができない
総合評価
品質:
力学的特性:
成型コスト:
量産性:
成型サイズ:
成型可能な形状の自由度:
寸法精度:
プルトージョン(引き抜き)法で製造されている具体例
建築資材
解説
プルトージョン法の最大のメリットは、連続的な生産が安定した品質で行えることです
一方、繊維配向や成型可能な形状に大きな制限があることがデメリットです
射出成型(インジェクション)って何?
射出成型は、熱硬化性樹脂と炭素繊維から作られた”ペレット”と呼ばれる中間基材を使用する成型法です
ペレットは下記の写真のように、粒状の中間基材です
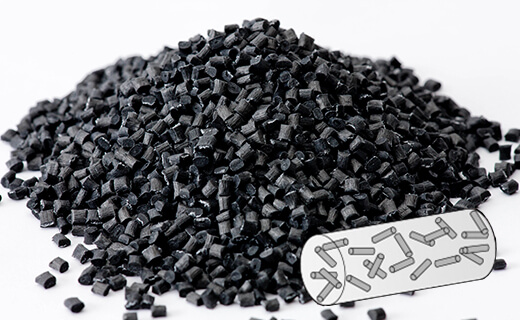
引用: 熱可塑性成形材料 | 熱可塑性複合材料 | 製品 | 炭素繊維複合材料 | TORAY (cf-composites.toray)
射出成型法
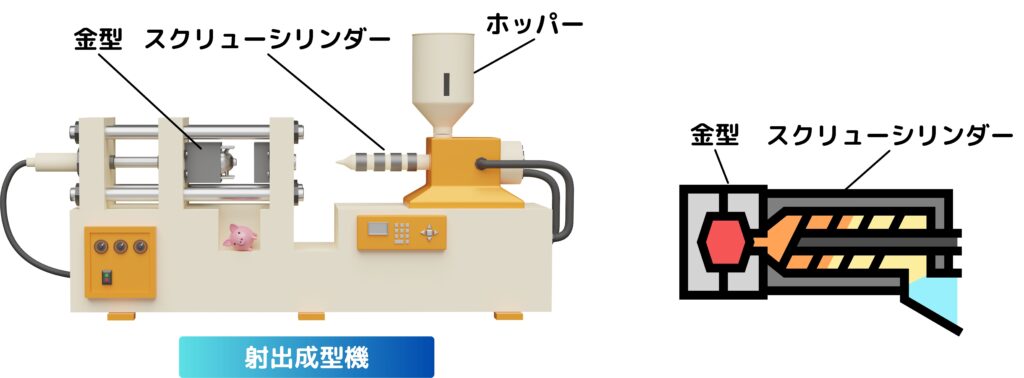
①ペレットを溶融し、加圧しながら金型内に注入する(射出)
②材料が硬化するまで圧力を保つ(保圧)
③材料を硬化させるため、金型を冷却する
④金型を開く
⑤材料を取り出す
メリット・デメリット
射出成型(インジェクション)法のメリット
- 高サイクルタイムで量産性が良い
- 自動化されているため品質が安定する
- 複雑形状の成型が可能
- 熱可塑性樹脂を使用するため、リサイクルが可能
射出成型(インジェクション)法のデメリット
- 力学的特性が低い
- 金型費が高い
- 寸法精度が低い(ひけ・そり)
総合評価
品質:
力学的特性:
成型コスト:
量産性:
成型サイズ:
成型可能な形状の自由度:
寸法精度:
射出成型(インジェクション)法で製造されている具体例
自動車などの小型部品
解説
射出成型によって作られる成型品は、炭素繊維が短くカットされている・繊維方向がランダムであるという二点から力学的特性が低いことがデメリットです
一方で、サイクルタイムや量産性は本記事で紹介した成型法の中で随一と言っても良いでしょう
従って、強度や剛性がそこまで必要なく大量生産する小型部品が射出成型に最も適しているといえます
まとめ
品質部門1位: オートクレーブ法
力学的特性部門1位: オートクレーブ法・シートワインディング法
成形コスト部門1位: 射出成型法
量産性部門1位: 射出成型法
成型サイズ部門1位: オートクレーブ法
成型可能な形状の自由度部門1位: 射出成型法
寸法精度部門1位: プレス成型法・RTM法